Beneficial Aspects of Industrial Electric Motors
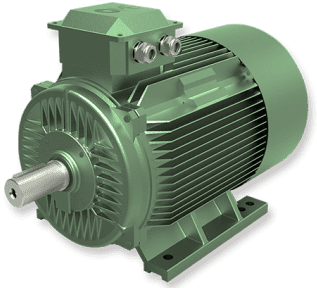
Industrial electric motors are essential components for many critical industries, as they efficiently convert electrical energy into mechanical power. This makes them important tools for minimizing operating costs. Energy efficiency rates for electric motors can exceed 90%. This is thanks to the use of quality materials and design optimisation approaches. By reducing copper loss (heat loss of current carrying windings), iron loss (heat loss of the motor’s iron core) and stray losses, these efficiency levels can be pushed further. Uncover the best rates for buy electric motors by clicking here or visiting our official website.
Considering that most industrial organisations are seeking to demonstrate their environmental concern, implementing an electric motor energy-efficient policy can be a great way to achieve this. In many cases, replacing older motors with more efficient models provides rapid payback times and can save a significant amount of energy over the lifetime of the machine. In order to improve the market availability of highly energy efficient industrial electric surplus motors , several countries have implemented minimum energy performance standards. As a result, these newer models are becoming increasingly available.
Electric motors convert electrical energy into a form of mechanical energy that drives machinery, equipment and vehicles. They are also extremely efficient, making them a vital component in efforts to reduce air pollution and combat climate change. The basic principle of how electric motors work is simple. The electric current flowing through the conductor creates magnetic fields that interfere with each other, producing a rotational mechanical force. These motors typically have two mechanical components, a fixed stator and a rotating rotor around the shaft. They also have two electrical components, a set of magnets and an armature, which together make up the magnetic circuit. A motor can produce a high level of precision depending on the size and design. For example, the length of the gap between the rotor and stator determines how accurate the motor is. The gap should be as small as possible, since a wide gap results in poor performance. Other special considerations include explosion-proof motors, used in hazardous environments such as oil refineries and gas production facilities.
Electric motors do not require as many mechanical components as combustion engines, which reduces maintenance costs and increases reliability. They also tend to operate quietly and produce very little vibration, making them a great option for industrial environments where noise and vibration can be disruptive or harmful. However, it is important to keep in mind that even electric motors need regular maintenance. It is crucial to have a process in place to identify issues before they become problems, which will save time and money by avoiding unnecessary downtime. For example, employees should regularly inspect the brushes and commutators to ensure they are not excessively worn or damaged. They should also check the fuses, cable connections and contactors for loose or bad contacts.
Comments
Post a Comment